When choosing a foundry, one has to make sure it is of the highest quality to avoid pitfalls in the engineering process such as casting defects. The proper design and molding from a trusted foundry can provide a defect free cast, but due to some control limitation and human interference, defects can always occur. Anything from defective pattern design, improper melting of metal, defective molding material or improper venting can cause defects and imperfections in a finished product.
Below we examine some common casting defects and how to determine if a finished piece is of high quality:
Blow – The blow is a relatively large cavity or hole produced by gases which displace molten metal’s form.
Scar – Due to improper permeability or venting, a scar is a shallow blow. It typically occurs on a flat surface.
Blister – A blister is a shallow blow like a scar, but with a thin layer or metal covering it.
Scab – This defect occurs in sand casting when a portion of the face of the mold lifts or breaks down and the recess left behind is filled by metal. When the metal is poured into the cavity, gas may be disengaged with such force as to break up the sand which is then washed away and the resulting cavity filled with metal.
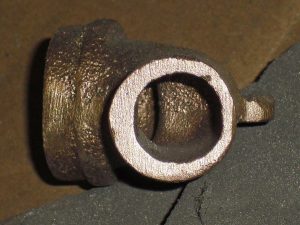
Core Shift – A core shift is a defect due to the buoyancy of molten metal where the core of a cast moves from where it was originally intended to be.
Mold Shift – A mold shift is caused by the mold cope itself shifting sideways relative to the drag. This results in a step or indent in the final cast at the parting line.
Drop – A drop is an irregularly shaped projection on the surface of a casting. This defect is caused by the break-away of a part of mold sand as a result of weak packing, low strength of the molding sand, malfunctioning of molding equipment, or strong jolts and strikes at the flask when assembling the mold. The loose sand that falls into the cavity will also cause a dirty casting surface, either on the top or bottom of the casting.
Penetration – Penetration is a strong crust of fused sand on the surface of a casting. When the molten metal is poured into the mold cavity, wherever sand packing was inadequate some metal will flow between the sand particles for a distance into the mold wall and get solidified. When the casting is removed, this lump of metal remains attached.
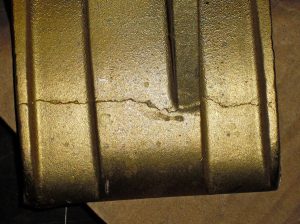
Buckle – A buckle is a long, broad shallow depression, that occurs in the surface of flat castings. It extends in a straight line across the entire flat surface.
Rat Tail – A rat tail is a long, shallow, angular depression in the surface and resembles a buckle, except it’s not shaped like a broad vee.
Pin Holes – Pin holes are small gas holes either at the surface or just below the surface. When these are present, they occur in large numbers and are fairly uniformly dispersed over the surface.
Wash – A wash or cut is a low projection on the drag face of a casting that extends along the surface, decreasing in height as it extends from one side of the casting to the other end.
Hot Tears – Hot tears are hot cracks which appear in the form of irregular crevices with a dark oxidized fracture surface. They arise when the solidifying metal does not have sufficient strength to resist tensile forces produced during solidification.
Shrinkage – A shrinkage cavity is a depression in a casting that results from the volume contraction that occurs during solidification.
Swell – A swell is a slight, smooth bulge usually found on vertical faces of castings, resulting from liquid metal pressure. It may be due to low strength of mold because of too high a water content or when the mold is not rammed sufficiently.
Any quality foundry will use inspection methods (often radiographic or ultrasonic) to make sure your finished product is defect free. Patriot Foundry not only maintains rigorous inspection standards, but has the expert staff and high-end equipment to ensure your casting quality is second to none.
If you are wondering what difference a quality casting can make for your application, contact us today!