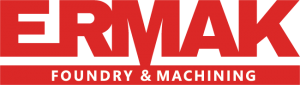
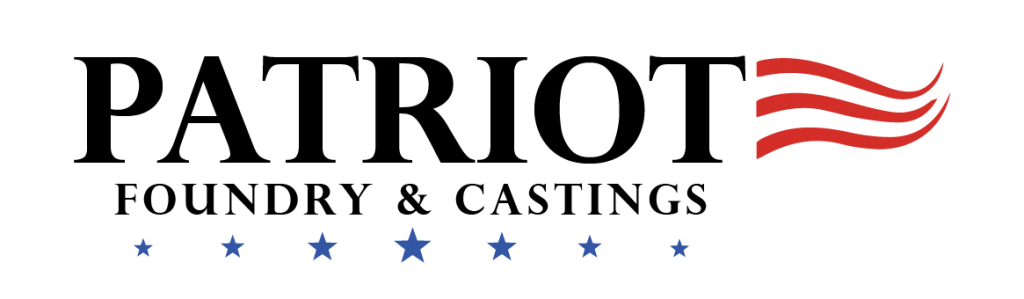
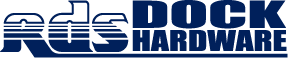
Ermak and Patriot Provide Expanded Foundry Capabilities to Customers
The combined offerings of Ermak Foundry & Machining (including the former Northwest Casting) and Patriot Foundry & Castings provide customers with expanded foundry capabilities. Existing and new customers benefit from the ability to produce nonferrous products from green sand, no-bake/air set, and permanent mold/gravity-fed die cast, as well as the associated services of machining, heat treating, precision grinding, painting, anodizing/plating, and assembly. Reg Zeller, owner of the combined businesses, commented, “We started on this journey four years ago because we fundamentally believe in local manufacturing. Patriot fit perfectly in our long-term strategy of geographic and capability expansion.” With hundreds of years of collective experience, diversified service offerings and additional resources to invest in state-of-the-art technologies, Ermak and Patriot can deliver scalable, small business customer service along with state-of-the-art production facilities usually seen only in large conglomerates.
We Take Care of Our Customers, Partners, Employees and Relationships
Chris and Debbi Leuteritz, Patriot sellers, turned the company around to make it a great organization. “There were two main reasons for us deciding to sell the company to Reg and the team he has assembled: values and vision,” Chris said. “We believed from our very first discussions that we shared values for how to run a business. It starts with people and relationships. If you take care of that—then service, production, quality, safety, and ultimately profitability follow. We care about our customers, partners, and employees and believe Reg and the team were the right fit to lead them into the future. When you put 13 years of your life into something, you want to see it prosper. We had plans to grow the business in a major way and believed Reg’s strategy and business acumen would be a good match for bringing it to the next level while remaining true to our values and vision.”
Experts in Casting Aluminum Brass, Bronze, Zinc and Other Copper-based Alloys
Ermak’s customer base is centered in the United States’ Midwest but spans North America and Europe. Ermak serves a wide range of manufacturing operations: transportation, infrastructure, outdoor sports and recreation, agriculture, automotive/racing, explosion/fireproof equipment, food, and hydraulics. Patriot serves customers all over the United States and Canada; however, most are in the Northeast of the United States. The Department of Defense, packaging, communications, aerospace, automobile, biotech, electronics, firefighting, medical, and imaging are just a few of the industries they serve. Seth Cutler, President across the organizations, mentioned, “The acquisition of Patriot was a logical next step after the integration of Northwest Casting’s permanent mold/gravity-fed die-cast and in-house heat treat capabilities last year. Our emphasis has expanded to other nonferrous alloys in tandem with the installation of our automated molding and sand testing systems. Patriot expands our aluminum capability geographically, as well as expertise in brass, bronze, zinc, and other copper-based alloys, plus the capability for assembly of complete parts.”
Seth Cutler is leading the effort at Patriot Foundry & Castings
Patriot’s history stretches back more than 50 years. Over the past decade, much of the melt and mold room was upgraded, focusing on energy efficiency and quality. Seth Cutler is leading the Patriot effort, “Our goal is to build on Patriot’s years of heritage pouring both aluminum and bronze alloys, to advance the employees’ training and knowledge base, increase the capabilities of the equipment and facility, and utilize the significant resources available through working closely with Ermak.”
Ermak is Growing its Regional and National Network and Expanding into New Markets
With new capabilities brought online by Patriot and their extensive partner network, Ermak will grow its regional and national network and expand into new markets. Patriot will have additional capacity, including rapid prototyping and part development through Ermak’s proprietary product development process and access to in-house heat treat, machining, and permanent mold/gravity-fed die cast. These new capabilities provide customers with a broader, more cost-competitive one-stop-shop for nonferrous castings. Eric Sloan, GM at Ermak with years of experience in operations and foundries at John Deere, said, “Ermak’s access to capital and experience adding automation across the enterprise allows for future expansion for Patriot and RDS Dock Hardware. With this acquisition, we will have nearly quadrupled the size of the company in four years. We’ve been focused on automating both the shop floor and back-office, so we have a strong foundation from which to scale the companies.”
Acquisition of RDS Dock Hardware is Part of Ermak’s Strategy to Provide Locally Produced Products
RDS Dock Hardware’s acquisition brings both Reg and Seth back to their engineering and product management roots. Reg and Seth met ten years ago when they were running parts of GE’s electrical business. RDS offers all of the individual and necessary components (high-quality, long-lasting aluminum cast components) to build new or expand/repair existing docks. RDS amenities including benches, beverage holders, flag holders, dock/boat cleats, and more. Due to the high quality of the products and ease of installation, RDS has a wide following in New England, with most sales driven by word of mouth. Recent expansions through dealers and e-commerce channels like Amazon continue to grow the business. Seth commented, “We immediately knew RDS was a great fit. Our strategy to have locally-made products matches perfectly with the fact that Ermak has nearly 25,000 lakes within a 300-mile radius of the foundry.” The team’s overall love for boating/cabin life and three decades of experience as engineers, product managers, and general managers in Fortune 500 companies will continue to take RDS to new heights.
RDS was founded in 1986 by Luther Drake with the aim of manufacturing rust-free cast aluminum components. Docks built decades ago with RDS hardware are still in great condition. RDS hardware is a one-of-a-kind deal that you won’t find anywhere else. Reg jokingly admits, “I’ve told my family and friends what we do for years. Only now are they excited that I can get them a dock to test out new prototypes. And the ideas they’ve had for years to make boating easier are pouring in, so we will have plenty of development coming.” RDS will continue its expansion using a network of sales reps and dealers from coast to coast. With engineering, product management, and capital access, RDS will now have the means to further expand its dock hardware line into many new areas including marine pedestals, boat lifts, and smart home integration.
Thank You NFFS & AFS for Sharing Our News!
Thank you, AFS, American Foundry Society, for including our press release in Modern Casting Magazine, A Publication of the American Foundry Society, and your digital newsletter Foundry Files.
NFFS, Non-ferrous Founders’ Society Industry Insider, thank you for including us in your publication to help share our news!